Home / Insights / EDI-ERP Integration in the Automotive Sector: The Risks of Not Having an Expert
Insights
Our perspective about the Automotive Supply Chain challenges
EDI-ERP Integration in the Automotive Sector:
Why Specialization Makes All the Difference
In a sector as dynamic and demanding as the automotive industry, where every minute counts and every failure can compromise the supply chain, the integration between EDI (Electronic Data Interchange) documents and ERP (Enterprise Resource Planning) systems, like SAP, is a cornerstone for ensuring predictability, traceability, and operational efficiency.
However, despite its importance, EDI-ERP integration projects are still frequently conducted without the direct involvement of specialists who have mastered the specific business rules of the automotive chain. And this is precisely where one of the biggest risks lies: when this specialization is not present from the functional design and ERP process definition phase, the operational and strategic impacts tend to appear—sooner or later.
When Integration Fails—Even While “Working”
Many projects may seem technically functional, with data being exchanged between systems, but without the critical rules being correctly applied. This creates a false sense of confidence, where errors are not immediately visible—but they have a direct impact on production planning, operational costs, and the reliability of information.
Some common examples include:
- Misaligned production due to incorrect interpretations of codes, deadlines, or volumes specified in EDI documents.
- Increased costs from emergency freight, overtime, or maintaining high inventory levels—to compensate for forecasting failures.
- Delays in the production chain due to inaccurate or poorly synchronized data between EDI and the ERP.
- Risks of contractual penalties and loss of trust with OEMs, caused by recurring failures and poor traceability.
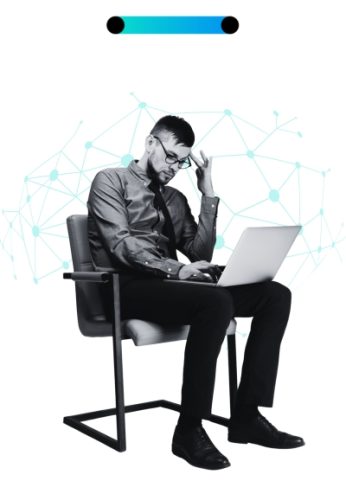
It All Starts in the Functional Design—and in the Details
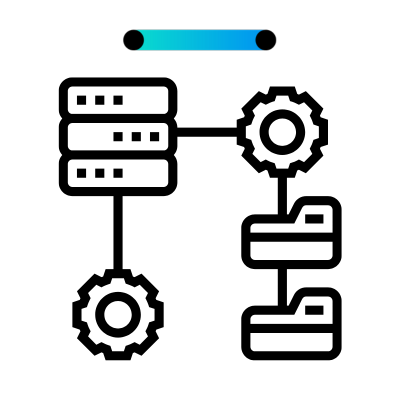
The ERP solution modeling phase (known in many projects as the blueprint) is when structural decisions are made. It is where the operation’s critical processes, business logic, integration rules, and workflows that will sustain the operation for years to come are defined.
If EDI-ERP integration is not considered strategically at this moment—with the active presence of a specialist—the risks increase considerably. The project runs the risk of moving forward with structural flaws such as:
- Inconsistencies between operational data and documents received from OEMs.
- Lack of visibility over exceptions or critical discrepancies, which get lost between poorly configured interfaces.
- Schedule delays and increased costs due to rework or late reconfigurations.
The Four Pillars of a Robust Integration
Successful EDI-ERP integration projects in the automotive sector share a solid foundation built on four main elements:
- Expert-Led Diagnosis The initial analysis must be performed by someone who masters automotive standards and understands the sensitive points of each flow. A specialist anticipates mapping failures, points out where data can be lost, and prevents exceptions from silently entering the ERP, which would compromise planning.
- Architecture Adapted to the Client’s Reality There is no single operating standard in the automotive sector. Each OEM has its own calendar, logistical rules, and document formats. Therefore, the integration architecture needs to be flexible and adhere to the client’s business model—without relying on artificial customizations or palliative solutions.
- Continuous Governance and Monitoring A successful integration is not sustained merely by the go-live event. It is necessary to ensure continuous data traceability, real-time exception management, updates according to OEMs changes, and training for the involved teams. Without this, operational failures will recur.
- Compliance with Industry Standards Companies that work with OEMs must meet strict requirements for quality, security, and information governance. Standards such as TISAX or SOC 2 are not just a formality—they directly impact the continuity of contracts and the company’s reputation in the global supply chain.
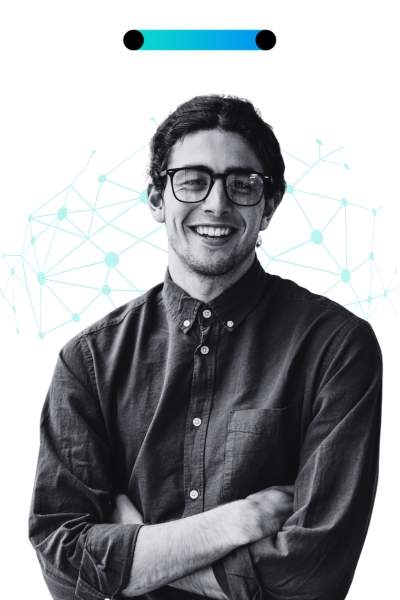
Integration as a Business Strategy
In summary, the integration between EDI and ERP should not be treated as an isolated technical task. It is a strategic decision that affects production, logistics, finance, and the customer relationship.
Projects that involve specialists from the beginning gain agility, robustness, and scalability. More than that, they avoid rework, reduce hidden costs, and deliver reliability to the business—the true asset for anyone operating at the heart of the automotive supply chain.
- Explore Sintel's Insights
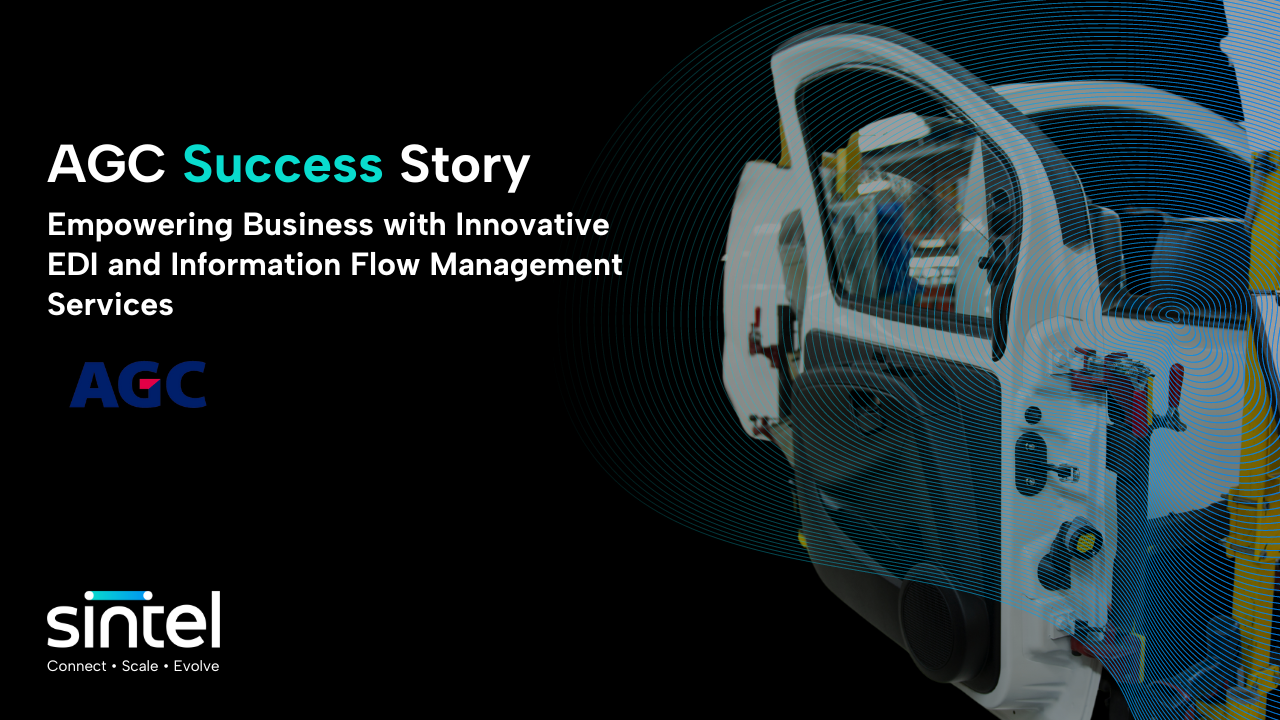
Empowering Business with Innovative EDI and Information Flow Management Services
Explore stories of companies that have successfully overcome challenges through the application of technology.